Статьи
Полиуретановые адгезивы для гибкой упаковки
В связи с тем, что в настоящее время законодательство многих развитых стран в области защиты окружающей среды и здравоохранения направлено на сокращение использования в промышленности веществ, содержащих летучие органические соединения, в мире гибкой упаковки обозначилась четкая тенденция перехода от клеевых составов для ламинации на основе растворителей в сторону клеевых составов на водной основе или безсолвентных (безрастворных) клеев со 100% сухим остатком. 100%-ый сухой остаток означает, что клеевой состав является моногамным по структуре и его отверждение наступает, как будет показано дальше, не за счет выпаривания основы (воды или растворителя), а за счет взаимодействия с другим веществом. Сами по себе водные клеи для гибкой упаковки могут представлять собой либо полиуретановые, либо акриловые дисперсии для "сухой" ламинации, известной как Dry-Bond.
Кроме этого растет популярность клеевых составов со 100%-м сухим остатком, которые содержат очень низкий уровень остаточных (свободных) мономеров. Почему наличие таких остатков в составе готового ламината является крайне нежелательным будет рассказано далее.
"Сухая" ламинация представляет собой процесс, при котором водный или растворный клей подается на поверхность ламинируемого материала, и из него выпаривается основа с помощью нагрева и потока горячего воздуха. Затем материал с полученным на его поверхности клеевым слоем, соединяется (ламинируется) со вторым материалом посредством подогреваемого прижимного вала. Процесс ламинации с использованием безсолвентного клея хорошо известен и выглядит несколько проще. На один из ламинируемых материалов через систему валов подается жидкий клеевой состав (вязкость около 2000 мПа по Брукфилду) и затем этот покрытый клеем материал соединяется со вторым материалом на таком же прижимном валу. Оба метода предусматривают создание довольно тонкого слоя клея весом около 2-3 граммов на кв.метр (в сухом виде), которого обычно хватает для того, чтобы готовый ламинат соответствовал всем необходимым параметрам межслойной адгезии и термостойкости.
Типичный состав производимых ламинатов представляет собой различные комбинации полимерных пленок (ПЭ, ПЭТ, ПС, ПП, ПА и др.), алюминиевой фольги, и иногда, бумаги. В основном, полученные 2 и 3-слойные ламинаты используются для производства пищевой упаковки. И хотя спектр их применения в этой области очень широк, существует всего несколько основных технических параметров, которые используются для оценки их качества. Все клеи должны обеспечивать хорошую адгезию и иметь очень высокую степень прозрачности после отверждения. Кроме этого необходимо, чтобы клеи эффективно сопротивлялись влаге и высокой температуре, которая требуется при сварке пакета по шву или термической обработке упакованного в него продукта.
Еще одним важным параметром клеевого слоя является его способность сопротивляться образованию дефекта, известного, как "туннелинг" - локальное расслоение 2-х ламинируемых материалов, внешне напоминающее морщины или складки на поверхности одного из них. Причиной такого дефекта, кроме некорректного соотношения натяжения ламинируемых полотен, являются либо разный коэффициент линейного теплового расширения или сжатия двух ламинируемых материалов либо разная скорость этих процессов. "Туннелинг" портит внешний вид упаковки и ухудшает ее защитные свойства. К сожалению, эта проблема широко известна в отрасли и с ней сталкиваются практически все производители гибкой упаковки.
Эмульсии на водной основе
Примерно, четверть мирового рынка клеев для гибкой упаковки составляют акриловые эмульсии или полиуретановые дисперсии. Поначалу, единственной причиной использования этих продуктов в промышленных масштабах было возросшее давление со стороны государственных органов в области охраны здоровья и окружающей среды. Постепенно появление на рынке новых "кросслинкеров" (веществ, которые связывают молекулы мономеров между собой в ходе реакции отверждения и отвечают за прочность образовавшегося полимера - прим. ред.), таких как растворимые в воде изоционаты, многофункциональные азиридины и ряд других позволило значительно улучшить адгезионные свойства клеев на водной основе и повысить их термостойкость, тем самым, сократив дистанцию между ними и клеями на основе растворителей. Использование подобных кросслинкеров в эмульсиях обеспечивает высокую адгезию между пленками и снижает вероятность образования "туннелинга".
Полиуретановые дисперсии
ПУР водные дисперсии по адгезии и термостойкости стоят ближе всего к традиционным растворным клеям. Они очень хорошо ведут себя на ламинаторе и позволяют работать с высокой скоростью. К тому же ПУР дисперсии обладают высокой прозрачностью после отверждения и вполне сопоставимы по этому параметру с лучшими солвентными клеями. Однако, недостатком подобных эмульсий является их стоимость. Полиуретановые эмульсии основаны на алифатических диизоционатах, не реагирующих с водой, которые значительно дороже толуольных изоционатов, которые используются при производстве растворных клеев.
Акриловые эмульсии
Представляют собой продукцию "эконом" класса, где сравнительно невысокие показатели адгезии компенсируются низкой ценой самого клея. Круг применения таких клеев ограничен простыми работами (одинаковые пленки и т.п.), к тому же они весьма сложны в использовании и требуют наличие охлаждающего цилиндра в конструкции ламинатора. Такой цилиндр предотвращает образование сгустков продукта. Эти эмульсии также имеют тенденцию пенообразования, что налагает ограничения на скорость работы ламинатора. Однако, сейчас на рынке имеются акриловые эмульсии, которые перерабатываются на скорости до 250 м/мин и при добавлении специальных "кросслинкеров" догоняют ПУР дисперсии по своим основным свойствам в готовом ламинате.
Процесс отверждения
При добавлении в водно-дисперсионный клей специальных "кросслинкеров" образовавшийся состав повышает способность готового ламината сопротивляться воздействию критических температур, что является важным моментом при изготовлении упаковки для горячего розлива, кипячения или хранения замороженных продуктов. Естественно, такой состав лучше сопротивляется эффекту "туннелинга".
Несмотря на то, что водные клеевые составы работают при повышенных температурах (около 100°С), нахождение их при этой температуре (в сушке) ограничено коротким промежутком времени. Поэтому предполагается, что реакция образования межмолекулярных связей (отверждение) в клеевом слое продолжается в готовом ламинате уже при комнатной температуре. В большинстве случаев готовый ламинат можно резать на требуемый формат почти сразу после ламинации. Несмотря на продолжающийся процесс отверждения, первоначальной адгезии вполне достаточно для проведения этой операции. Такая особенность технологии Dry-Bond существенно экономит время, по сравнению с широко применяемой технологией безсолвентной ламинации.
Безсолвентные клеевые композиции со 100% сухим остатком
Клеи первого поколения
Первые появившиеся на рынке безрастворные полиуретановые клеи отверждались под воздействием влаги. Эти клеи производятся и сейчас и используются, главным образом, в тех структурах, которые содержат в себе влагу (бумага, картон, ПА), и которые не являются прозрачными. Они состоят из преполимеров изоционатов и обладают высокой вязкостью, что обеспечивает хорошее первоначальное схватывание. Одним из недостатков этих клеев является высокая температура нанесения, 90-100°С. Клей подается на поверхность материала тонкой пленкой и избыточный изоционат реагирует с атмосферной влагой, в ходе чего в нем начинают образовываться перекрестные молекулярные связи. Затем, прикатывается второй материал (происходит ламинирование) и реакция отверждения продолжается уже в готовом роле. Резку этого роля на требуемую ширину рекомендуется начинать не ранее, чем через 24-72 часа. Схематично реакция полимеризации клея первого поколения может быть представлена пошагово формулой:
R-NCO + H2O ---- R-NH2 + CO2
R-NH2 + R'-NCO ---- R-NHCOHN-R'
Основные проблемы, связанные с использованием клеев первого поколения - это, как видно из указанной выше формулы, образование двуокиси углерода в процессе полимеризации, и ее выделение в виде мельчайших пузырьков, а также появление замутнения на прозрачных пленках и непостоянство сроков полимеризации. Проблема образования пузырьков углекислого газа встает особенно резко при использовании высокобарьерных пленок. Дефект замутнения пленки и непостоянство времени протекания реакции возникает и зависит от количества влаги, которая вступает в контакт с клеем. Влага обычно подается через распылитель на первичную пленку после нанесения на нее клея и непосредственно перед соединением со второй пленкой. Дополнительная порция влаги естественно ускоряет процесс отверждения клея, но ведет к появлению замутнения, которое хорошо заметно только на прозрачных пленках. Именно поэтому клеи первого поколения не рекомендуются к использованию в прозрачных структурах, но с успехом применяются в структурах, содержащих картон или бумагу.
Клеи второго поколения
Следующим большим шагом в развитии технологии безсолвентных клеев стало появление двух-компонентных клеевых составов. Такая система традиционно состоит из полиуретанового преполимера и полиоли. Оба вещества имеют довольно низкую вязкость. Их смешение осуществляется при комнатной температуре, и, затем, смесь закачивается на наносящий узел ламинатора через встроенный статический миксер. Хотелось бы отметить, что в двух-компонентных системах следует уделять повышенное внимание правильности пропорций смешения. Например, в США специалисты традиционно рекомендуют работать с "избытком" изоционата. Говоря о популярной там клеевой системе Lamin WD-4120/22 пропорция изоционата в смеси 1:1 не обеспечивает должной адгезии и, как следствие, термостойкости готового ламината.
Пропорция 2:1 (двойное превышение изоционата) сильно растягивает во времени процесс отверждения. Поэтому опытным путем на основе лабораторных анализов было выявлено, что пропорция смешения с избытком изоционата 1,2:1 (весовое соотношение) делает свойства смеси WD-4120/22 оптимальными: термостойкость готового ламината находится на максимуме, а процесс полимеризации полностью завершается через 48 часов. При этом, операцию резки готовых ролей на требуемый формат можно начинать через 12-24 часа. Именно это клеевая система считается сейчас самой "быстрой" на рынке.
Механизм отверждения двух-компонентных клеев представляет собой следующий процесс:
R-NCO + HO-R' ---- R-NHCOO-R'
Двумя основными проблемами этих продуктов является низкая первоначальная вязкость композиции и, как следствие, низкое первоначальное схватывание и сравнительно высокий уровень остаточных мономеров после завершения процесса полимеризации. Низкое схватывание создает необходимость повышенного контроля процесса ламинации, чтобы избегать "туннелинга". Резка готовых ролей может производиться не ранее чем через 12-48 часов. Высокое содержание остаточных мономеров ведет к их миграции сквозь мягкие "сварные" пленки типа полиэтилена и их реакции с атмосферной влагой.
Таким образом, на поверхности мягкой пленки создается тончайшее термостойкое полиуретановое покрытие, которое либо значительно затрудняет процесс сварки, либо делает его вообще невозможным. Естественно, кроме сугубо технических проблем, возникающих в связи с образованием данного слоя, возникает потенциальный риск попадания молекул изоционата в упакованный продукт. Следует отметить, что мигрирующие мономеры также создают риск для здоровья рабочих в цеху, в особенности тех из них, кто осуществляет резку и упаковку готовых ламинатов.
Для устранения указанных проблем были разработаны клеи третьего поколения, которые обладают высоким первоначальным схватыванием, постоянством процесса отверждения и имеют сравнительно низкий уровень остаточных мономеров.
Клеи третьего поколения
Клеи третьего поколения основаны на полиуретановых полимерах с большим молекулярным весом и соответственно большей вязкостью и перерабатываются при температурах 50-70°С. Повышенная вязкость таких клеев улучшает свойство их первоначального схватывания и операцию по резке на требуемый формат можно начинать через 12-24 часа. Уровень остаточных мономеров в смеси не превышает 0,08%, что достигается за счет особенностей механизма полимеризации.
Оборудование для ламинирования
Nordmeccanica (Италия) |
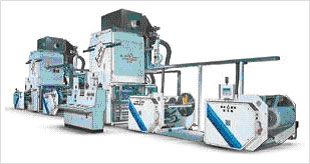 |
Универсальный ламинатор для изготовления трехслойных материалов
Triplex Combi. Ширина рулона 1100–1600 мм. Диаметр 850, 1000, 1200 мм.
Скорость до 400 м/мин. |
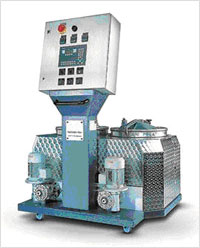 |
Станция смешения двухкомпонентного бессольвентного клея World Mixer.
Отвечает за точность температуры компонентов, правильное их соотношение, своевременность подачи клея. |
Ламинаты, благодаря их разнообразным свойствам, становятся все более популярным упаковочным материалом. И многие предприятия задумываются о внедрении того или иного способа ламинирования.
Если сравнить ламинаторы разных производителей, то, на первый взгляд, не будет заметно больших отличий. Только пристально всмотревшись, вы обнаружите удивительно много различий в конструкции, концепции, по числу моделей и дополнительных устройств. Это делает выбор очень трудным и долгим. Огромное количество итальянских поставщиков не облегчает принятие решения, но позволяет из большого многообразия моделей выбрать именно ту, которая вам требуется.
Еще несколько десятков лет назад ламинирование упаковочных материалов и нанесение покрытий на них были доступны только крупным производителям упаковки и полиграфическим предприятиям со специальным оборудованием. Основным способом ламинации был сольвентный (с применением клеев, содержащих растворители). Остальные изготовители упаковки при необходимости вынуждены были обращаться с размещением заказов к крупным производителям, имевшим соответствующее оборудование. Такой порядок приводил к удорожанию готовой продукции и к увеличению сроков ее изготовления.
Положение стало меняться примерно 20 лет назад после изобретения и внедрения в производство бессольвентного клея (не содержащего растворители). Эти клеи не сразу заняли свое место в производстве упаковки. Для их использования потребовалось изменить существовавшие ламинаторы, приспособив их к использованию однокомпонентного и двухкомпонентного бессольвентных клеев. Имевшиеся тогда секции нанесения клея не позволяли наносить очень тонкий и ровный слой на большую поверхность пленки или фольги. Более того, требовалось несколько суток, прежде чем происходило химическое закрепление клея и материал был готов к дальнейшему использованию. По этой причине первоначально бессольвентные клеи не могли использоваться в существующих устройствах для ламинирования гибкой упаковки. Преимуществом бессольвентного способа ламинирования было отсутствие необходимости устанавливать специальные системы сушки и, следовательно, значительная экономия по сравнению с сольвентным способом.
Производители очень быстро отреагировали на появление новой технологии и очень скоро представили свои разработки бессольвентных ламинаторов. В 1988 г. итальянская компания Nordmeccanica подала патентную заявку на секцию нанесения бессольвентного клея и в 1988 г. продемонстрировала ее своим клиентам. Наступила эра бессольвентной ламинации.
Что и чем ламинировать?
Schiavi (Италия) |
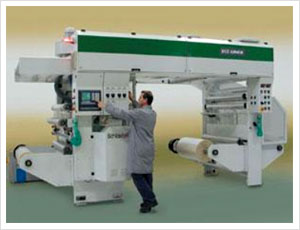 |
Бессольвентный ламинатор Eco Junior. Ширина 850–1450 мм.
Макс. диаметр рулона 1000 мм. Скорость 300 м/мин. |
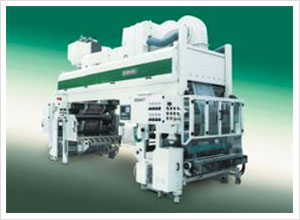 |
Универсальный ламинатор Ecoflex. Стандартная ширина материала
1150–1350 мм. Диаметр рулона 1000 мм. Скорость 300 м/мин. |
Для принятия решения о покупке ламинатора нужно решить следующие вопросы:
- Какие материалы будут склеиваться: полимерные пленки, металлическая фольга, бумага, картон?
- Каков конечный продукт ламинирования: двух- или трехслойный ламинат, его свойства и параметры (в частности, толщина), необходимость лакирования, нанесения воскового покрытия, печати и т. д.;
- Какой тип клея/клеев предполагается использовать для изготовления конечного продукта (бессольвентный: одно- или двухкомпонентный, сольвентный: на водной основе или на другой основе, клей УФ-отверждения);
Эти вопросы показывают, что имеется много вариантов ламинирования, соответственно, приобретаемый ламинатор должен «уметь» выполнять требуемые работы по всем параметрам заказчика.
Минимальная стоимость ламинатора — около 100 тыс. евро, максимальная цена доходит до 3 млн. Такой ламинатор, по сути, является мини-заводом с большими возможностями (до 11 опций), на котором можно выполнять любые существующие в настоящее время технологии ламинирования.
Большое число производителей ламинаторов и выпускаемых ими моделей затрудняет правильный выбор. Покупателю следует осторожно относиться к рекламе отдельных компаний, желающих во что бы то ни стало продать свой товар в России. Важным условием является способность осуществлять техническое обслуживание продаваемых ламинаторов. И, конечно же, нужно помнить, что в соотношении «цена — качество» цена является только одним из двух компонентов.
Бессольвентные ламинаторы
Comexi (Испания) |
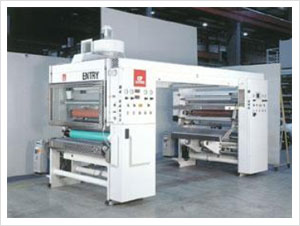 |
Бессольвентный ламинатор Entry 1300. Макс. ширина 1315 мм. Макс.
диаметр рулона на размотке 800 мм. Макс. скорость 300 м/мин. |
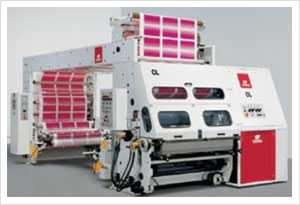 |
Бессольвентный ламинатор CL. Макс. ширина полотна 1070, 1370, 1470 мм.
Диаметр рулона 800, 1000 мм. Скорость 300 м/мин. |
Так называют ламинаторы, в которых используются только бессольвентные клеи. Клеи могут быть двухкомпонентными или однокомпонентными, они не требуют специальной тепловой сушки.
Основными узлами бессольвентного ламинатора являются: два размотчика, намотчик, узел нанесения клея, узел ламинирования и так называемый мост — секция, по которой полотно с нанесенным на него клеем движется от узла нанесения клея к узлу ламинирования. Мост может быть вертикальным или горизонтальным.
Отсутствие системы сушки позволяет значительно экономить на стоимости энергоносителей (до 30%). Бессольвентный способ ламинации является экологически более чистым чем сольвентный, так как в нем отсутствуют растворители.
Размотчики и намотчики могут быть с ручной и с автоматической установкой и снятием рулонов. Вес рулонов на отдельных моделях ламинаторов достигает 1200 кг, а диаметр — 1000 мм.
Узел нанесения бессольвентного клея — это система валов, из которых два являются дозирующими: между ними заливается клей и происходит его первичная дозировка. Трансферный вал переносит клей на кроющий вал, с которого клей наносится на рулонный материал. Различные производители предлагают разные технические решения этого узла, от которых во многом зависит равномерность нанесения клея и прозрачность материала. Валы представляют собой обогреваемые цилиндры, которые поддерживают необходимую температуру клея.
На узле ламинирования происходит «встреча» двух полотен и их склеивание. Перед узлом ламинирования или после него (в зависимости от технологии производства ламината) может быть установлен охлаждающий цилиндр.
После ламинирования склеенный материал перематывается на намотчик, а затем отправляется на выдержку. Минимальный срок ее составляет 24 ч, после чего рулон можно разрезать и перематывать без потери качества. Физическая полимеризация клеевого слоя наступает через 5–7 дней, химическая полимеризация может закончиться только через 7–14 дней после изготовления ламината. Фактор времени имеет большое значение для прочности склеивания.
Отдельным узлом является станция смешения бессольвентного двухкомпонентного клея. В ней оба компонента — смола и отвердитель — нагреваются до определенной температуры и подаются по раздельным обогреваемым шлангам в головку смешения, из которой готовый к употреблению клей поступает в узел нанесения клея.
Для бессольвентного ламинатора критическим фактором обеспечения качества ламината является система контроля натяжения. Любой сбой в этой системе приводит к появлению брака. Особенно важно, чтобы ламинатор обеспечивал синхронизацию работы всех двигателей и приборов контроля (тензодатчики, плавающие валы).
В качестве дополнительного оборудования можно рассматривать установку для обработки материалов коронным разрядом (коронатор), которая устанавливается непосредственно на ламинаторе. Она позволяет повысить поверхностное натяжение ламинируемого материала (одного или обоих) до приемлемого.
Бессольвентная ламинация развивается очень быстрыми темпами. Главное ограничение в применении бессольвентных клеев — их недостаточная термоустойчивость, что заставляет производителей использовать сольвентные. Бессольвентные клеи позволяют экономить не только на энергоносителях. Расход таких клеев колеблется в диапазоне 1–8 г/м2, можно наносить очень тонкий слой без ущерба для качества ламината. Экономия достигается также за счет отсутствия затрат на растворители. В целом бессольвентные клеи более экономичны, чем сольвентные.
Универсальные ламинаторы
Soma (Чехия) |
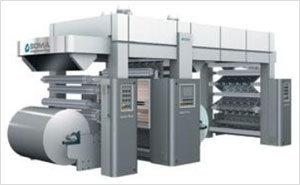 |
Бессольвентный ламинатор Lamiflex. Макс. ширина 1350 мм. Макс. диаметр
рулона 1000 мм. Макс. скорость 300 м/мин. |
Bielloni (Италия) |
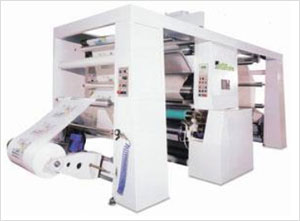 |
Бессольвентный ламинатор Julia Seconda. Ширина рулона 1280, 1480,
1680 мм. Макс. диаметр рулона 800 мм. Макс. скорость 300 м/мин. |
Бессольвентные ламинаторы нельзя использовать для ламинирования клеями на основе растворителей. Их технические и конструкционные особенности не позволяют применять сольвентный способ ламинирования. Отличительная особенность сольвентных ламинаторов — наличие специальной сушильной секции. В зависимости от способа нагрева воздуха, используемого в сушильной секции, можно выделить следующие типы сушек: электрические, масляные, газовые и паровые. На западе большим спросом пользуются ламинаторы с газовыми горелками, в связи с более низкой стоимостью газа по сравнению с электрической энергией.
Кроме типа сушки важно определить, для какого способа ламинирования предназначен ламинатор. Существует два таких способа: «влажное» и «сухое» ламинирование. При влажном ламинировании (wet lamination) оба материала склеиваются, когда клей находится во влажном состоянии. Такой способ ламинирования имеет ограниченное применение: главным условием для влажного ламинирования является пористость одного из склеиваемых материалов — как правило, это бумага или картон. Пористость материала позволяет испариться растворителю, содержащемуся в клее. Таким способом можно ламинировать, например, фольгу с бумагой, но нельзя — фольгу с целлофаном, так как растворитель не сможет испариться. При влажной ламинации узел сушки размещается после узла ламинации. Преимущество влажного ламинирования — высушивание многослойного материала в ламинаторе. По сравнению с уже упомянутой технологией бессольвентного ламинирования, когда полная полимеризация материала занимает довольно продолжительное время, этот способ позволяет ускорить срок изготовления ламината. Как правило, в процессе влажного ламинирования применяют клеи на водной основе.
При сухой ламинации (dry lamination) испарение растворителя происходит в сушильной секции до узла ламинации.
Имея в виду быстрое развитие бессольвентной ламинации, появление новых клеев, позволяющих заменить сольвентные, есть смысл выбирать универсальный ламинатор, позволяющий работать с разными клеями и покрытиями. Универсальные ламинаторы позволяют применять различные технологии ламинирования с помощью сменных секций нанесения клея. Достаточно сменить, скажем, бессольвентную секцию на секцию глубокой печати, провести очистку узлов и валов ламинатора от остатков клея — и ламинатор готов к смене работы. Причем на смену заказа не требуется много времени. Такая мобильность позволяет предприятиям быстро реагировать на меняющийся спрос и быть готовыми к выполнению заказов любой сложности. При работе с бессольвентными клеями на универсальном ламинаторе система сушки отключается.
Универсальные ламинаторы можно использовать не только для ламинирования бессольвентными и сольвентными клеями, клеями на водной основе и клеями УФ-отверждения, но и для нанесения покрытий: лакирования или печати с приводкой. Имеются модели, позволяющие наносить парафин, микровоск и ПВДХ, а также выполнять ламинирование микровоском.
Установка двух ламинаторов в линию позволяет получить триплексы (материалы, состоящие из трех слоев, например, бумага/фольга/пленка). В такой линии можно использовать два универсальных ламинатора или универсальный и бессольвентный ламинаторы. Такая конфигурация позволяет использовать различные виды ламинирования или нанесения покрытий, к тому же дает возможность приклеивания третьего материала как к первичному слою двойного ламината, так и к его вторичному слою при использовании переворотной секции. Такая линия несколько дешевле, чем один ламинатор для тройного ламинирования.
Дефекты при ламинации пленок
При производстве многослойной гибкой упаковки отдельного внимания заслуживает этап ламинации 2-х или 3-х гибких пленок или фольги между собой. На первый взгляд этот процесс кажется сравнительно простым. На самом деле ламинация пленок – это очень важный этап отделки готовой продукции, от его результата во многом зависят физические свойства полученной упаковки.
В ходе ламинации ПЭТ с инверсной печатью и металлизированного ПП возникает оптическое явление, которое хорошо заметно на белом фоне. Речь идет о появлении “крапчатости” или “апельсиновой корки” на фоне белого цвета. Это явление возникает и на других цветах, но лучше всего его видно именно на белом фоне. Это оптическое явление является следствием плохой смачиваемости клеем поверхности металлизированного полипропилена или, в ряде случаев, алюминиевой фольги. Заметным этот дефект становится иногда через сутки после ламинации.
Сегодня эта проблема считается типичной в отрасли, и основным средством борьбы с ней являются повышение температуры клеевой композиции при подаче, снижение скорости прохождения материала через ламинатор (иногда это скорость сокращается в 2 раза), увеличение объема подачи клея (в среднем на 40-60%), а также, но реже всего, настройками валов на самом ламинаторе. В целом это явление требует повышенного к себе внимания со стороны технолога по ламинации и оператора ламинирующего устройства.
Рекомендации по эксплуатации УФ ламп
Несмотря на то, что стоимость УФ ламп составляет лишь незначительный процент от общей стоимости флексографского процесса производства, УФ лампы являются ОДНИМ ИЗ ВАЖНЕЙШИХ ФАКТОРОВ в достижении надлежащего и полного отверждения УФ красок, лаков и других покрытий. Правильная техническая эксплуатация и своевременная замена УФ ламп позволяет избежать потенциально возможного удорожания процесса производства.
1. Соблюдение сроков эксплуатации
При нормальной эксплуатации УФ лампа служит около 1000 часов при максимальной нагрузке и 100% мощности. Через 1000 часов работы мощность лампы начинает снижаться, что постепенно приводит к неровному и неполному высыханию краски или покрытий. Рекомендуется производить замену лампы после 1000 часов работы. Использованные лампы могут храниться на случай крайней необходимости их дополнительного использования. Однако, несомненно, лучше использовать в таких случаях новую лампу, заранее подготовленную для замены.
2. Соблюдение режимов работы лампы
* Наибольший ущерб причиняется лампам при их частом включении и выключении. Во время технического перерыва (при обслуживании оборудования, смене вида работы и т.п.) наиболее благоприятным для лампы является режим ожидания/ простоя. Для перехода лампы из состояния ожидания в режим максимальной мощности требуется не более 2 секунд. При выключении оборудования и последующем включении процесс выхода лампы на режим полной мощности занимает около 5 минут. Если технический перерыв продолжается 1 час и более, тогда рекомендуется выключение машины/ оборудования. При продолжительности простоя менее 1 часа переводите лампы и оборудование в режим ожидания.
* Никогда не стоит брать лампу за соединительные провода, воспользуйтесь цоколями.
* Когда лампа устанавливается в корпусе необходимо убедиться, что ничто не касается колбы лампы: термопары, отражатель и т.д.
* Следует избегать резких скачков напряжения, а также отключения электропитания лампы и оборудования во время работы, так как это ведет к необратимым изменениям лампы (вздутие колбы, перегорание контактов и т.д.).
3. Обязательное фиксирование параметров процесса
Обязательно фиксируйте параметры системы: скорость печати, ресурс работы лампы, график технического обслуживания и т.п.
При возникновении проблем гораздо проще выявить причину и смоделировать процесс, если Вы обладаете выше перечисленной информацией.
4. Предотвращение перегрева
Охлаждающая система и система выпуска отработанного воздуха могут послужить причиной неэффективной работы УФ облучения. Всасывающие фильтры могут засориться, что в свою очередь приведет к перегреву лампы и ее преждевременному выходу из строя. Перегрев лампы можно визуально определить по ее прогибу (деформации).
5. Предотвращение переохлаждения
Переохлаждение может привести к столь же большому перечню проблем, как и перегрев. Температура кварцевого элемента должна быть в интервале 600-800 градусов Цельсия. Если температура опускается ниже обозначенного предела, пары ртути начинают конденсироваться в ее жидкое состояние, и эффективность работы лампы будет падать. Наиболее очевидный признак переохлаждения лампы – это длительный прогрев лампы до рабочего состояния. Лампа может погаснуть при выборе слишком низкого уровня мощности. Вы можете заметить, что лампа работает не так ярко, как при нормальном режиме.
6. Чистка ламп
После установки лампы в оборудование и перед ее первым включением рекомендуется протереть/ очистить поверхность колбы лампы. Не рекомендуется прикасаться к лампе голыми руками, всегда пользуйтесь хлопковыми перчатками. При случайном касании лампы голыми руками необходимо протереть лампу специальной салфеткой. Чистку ламп следует осуществлять специальными салфетками, прилагаемыми к лампе при поставке, либо для этой цели можно использовать изопропиловый спирт и чистую салфетку.
Если лампа устанавливается в оборудование и включается без предварительной чистки или длительное время функционирует, и на ней осаждается значительное количество внешних загрязнений, это может привести к расстеклованию лампы в загрязненных местах. К сожалению, процесс расстеклования нельзя остановить путем чистки лампы после того, как он уже начался.
Загрязнения часто приводят к преждевременному выходу лампы из строя.
7. Чистка рефлекторов
Чистку рефлекторов (отражателей) следует осуществлять при каждой замене/ установке новой лампы, но не реже, чем 1 раз в год. Это обеспечивает максимальную концентрацию светового потока на поверхности запечатываемого материала и способствует правильному охлаждению лампы. При невозможности очистки рефлектора или восстановления его правильной формы полностью замените его.
Металлическая пружина для переплета
Расходным материалом для металлического переплета является
металлическая пружина. Она может быть разного диаметра, с разным шагом, может
быть в промышленной намотке (бобинах) и уже порезанные под формат А4 по длинной стороне (форматные), и конечно большой выбор
цвета: белый, черный, серебро, бронза, синяя, красная, зеленая.
Для использования металлической пружины в больших объемах
(например, для изготовления большого тиража календарей или тетрадей) более
целесообразно использовать металлическую пружину в бобинах, поскольку она
обойдется значительно дешевле, чем форматная, и при использовании на
нестандартных форматах отходов будет значительно меньше.
Если же пружины нужны в небольших количествах, например для
использования в офисе, чтобы время от времени делать стандартные переплеты А4 или А5 формата, то переплачивать за целую бобину нет
никакого смысла.
При выборе металлической пружины необходимо знать:
- какой шаг имеет биндер, с помощью которого вы будете осуществлять переплет;
- высота переплетаемой стопы (или количество листов и какой плотности), чтобы правильно определиться с диаметром пружины,
- количество переплетов (тираж), чтобы экономично подобрать «фасовку» пружины (бобины или форматные).
Переплет на металлическую пружину отличается от пластикового
переплета более высокой ценой. Поэтому он реже используется в офисах и чаще
всего применяется для изготовления календарей, блокнотов, тетрадей.
Однако переплет на металл имеет целый ряд своих преимуществ:
- высокая прочность и практичность в использовании,
- возможность полного разворота брошюры на 360 градусов,
- презентабельный вид изделия,
- подходит как для офиса, так и для профессионального применения.
Переплет на металлическую пружину на первый взгляд имеет
много общего с пластиковым переплетом. Отличие – в технологии процесса
изготовления такого переплета, а именно – в процессе непосредственного переплета
брошюры.
При пластиковом переплете нужно сначала раскрыть пружину,
потом «одеть» брошюру, после чего пружина возвращается в исходное положение.
При желании ее снова можно раскрыть, добавить или наоборот, убрать листы и
закрыть, чего не сделаешь при металлическом переплете.
Металлические пружины раскрыты изначально,
ее в ручную нанизывают на брошюру, и после этого зажимают с помощью специальных
тисков на биндере, добавить или удалить какие-то листы из нее практически
невозможно.
Поэтому, для осуществления переплета на металл необходим
специальный аппарат – биндер на металлическую пружину. Во-первых, у него будут
тиски, вместо переплетной гребенки (как у биндра на пластик), во-вторых, такие
биндеры на металл отличаются формой (квадратное, круглое) и количеством
отверстий на 1 дюйм, пробиваемых этим биндером, что и называют шагом перфорации (3:1, 2:1).
Шаг перфорации 3:1 – 3 отверстия на 1 дюйм (на А4 формат по большой стороне приходится 34 отверстия).
Металлическая пружина с таким шагом является самой распространенной. Такие
пружины предполагают переплет стопы толщиной только до 12 мм (120 листов 80 г/м²), большую толщину пружина с таким шагом просто не выдержит
и будет разгибаться.
Шаг перфорации 2:1 – 2 отверстия на 1 дюйм (на А4 формат по большой стороне приходится 23 отверстия). С
помощью пружины с таким шагом можно переплести стопу до 280 мм (до 280 листов 80 г/м².
Основные характеристики, которые необходимо учитывать при выборе биндера на металлическую пружину:
- шаг перфорации (3:1, 2:1) при выборе шага вы будете руководствоваться тем, какие металлические пружины (с каким шагом) вы планируете использовать,
- максимальная толщина перфорации за один раз, это может отразиться на скорости изготовления переплета,
- регулировка глубины перфорации, важно при переплете большого количества листоотключение ножей, эта функция важна в основном для тех, кто собирается использовать биндер
для производства календарей, блокнотов, тетрадей, (чаще это не А4 формат, возможно частичный переплет, состоящий из отрезков
пружины, в календарях – как правило, по центру отключается 3 ножа, для того,
чтобы оставить место для высечки под календарную вешалку и т.д.,
- ограничение по формату на перфорацию, если вы планируете делать переплет на формат больший
А4, но покупаете биндер с шириной перфорации до 340 мм, это возможно только
если есть возможность перфорации на «вылет» (нет ограничения на перфорацию).
|